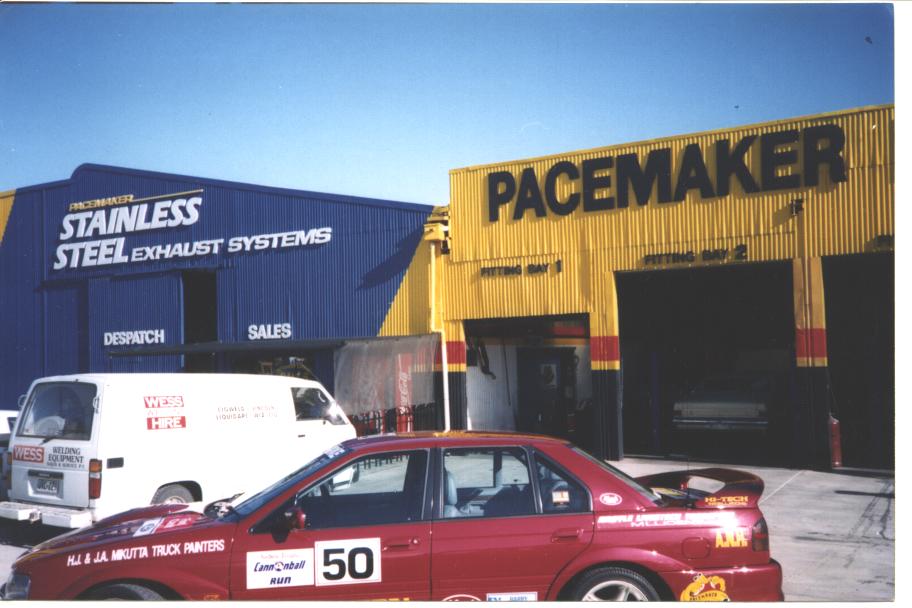
A long standing legacy
Performance exhausts made by aussies
For over half a century, PACEMAKER has been innovating, designing and manufacturing quality exhaust headers in Australia. Pacemaker was the first company to introduce mandrel-bending technology into the exhaust header market, forever changing the header industry landscape.
Today PACEMAKER still draws upon its long tradition of innovation by introducing new technologies into the market place. In this time Pacemaker has been able to design and build one of Australia's largest 4-into-1 and Tri-y catalogues. In 1997 Pacemaker introduced its turbulence eliminating 'Pipe Over Cone™' technology (design copyright number 135712). This advance in design and construction not only dramatically improves flow through the exhaust but also helps to lengthen the life of the product.
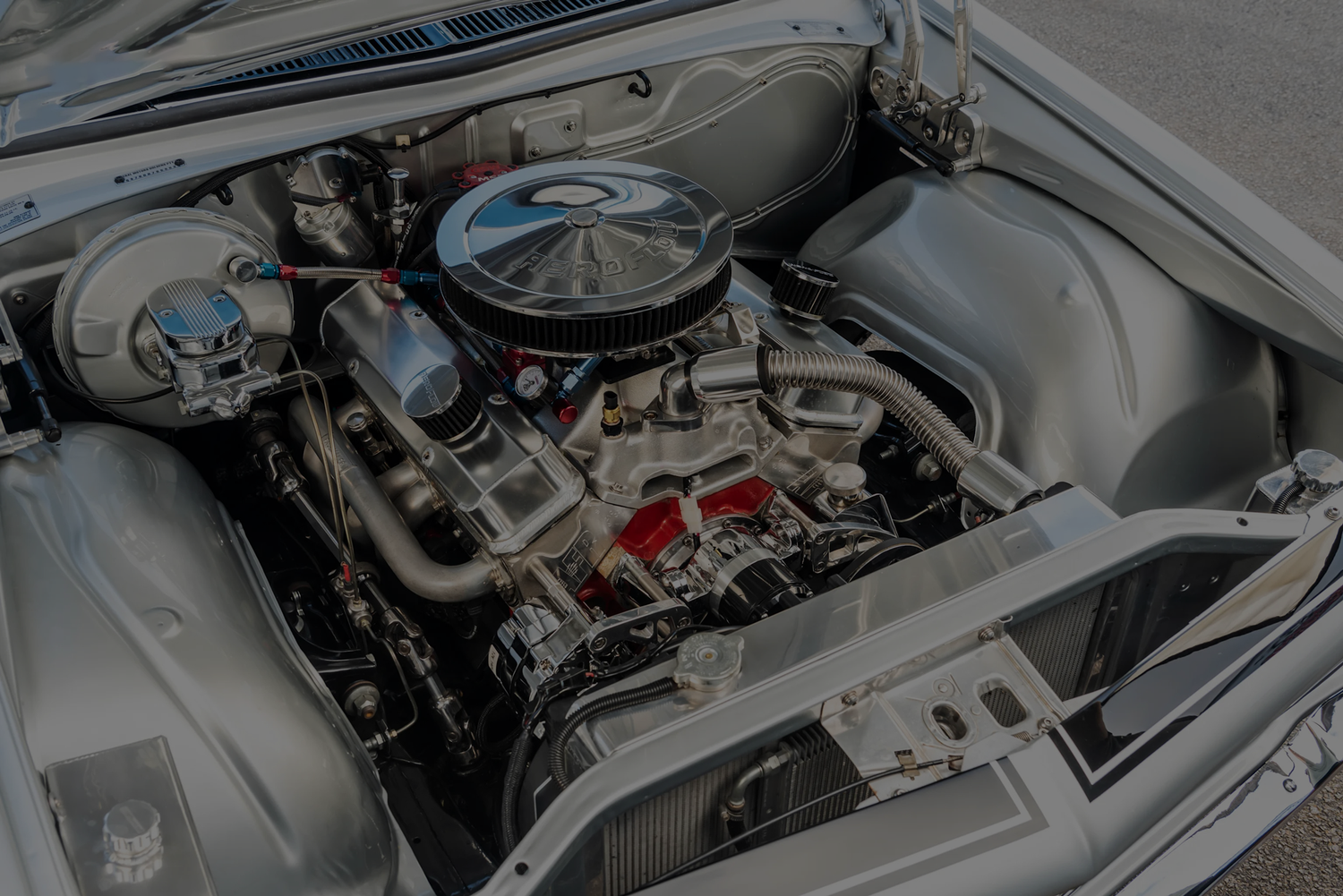
The Pacemaker Advantage
Pioneers of quality headers featuring the “Mandrel Bend” System.
Our modern workshop incorporates the very latest equipment available, including our aircraft quality computerised Benders with revolutionary, patented, vertebrate type mandrel, ensuring perfectly round bends, previously unavailable in Australia.
Additional Features Include
- Precision Laser cut and machined thick flanges to eliminate leaking and warpage.
- All headers are jig welded for guaranteed fitment and are checked prior to shipment.
- Comprehensive fitting instructions with V8 sets together with hi-tensile header bolts.
- Big bore pipes available for most popular V8 models.
- Emission hook-ups provided where applicable.
- Primary pipes fitted through the flanges.
- Heat proof finish tested to 1270°.
- Secondary and outlet pipes fitted over primary and outlet cones.
- Pacemaker are the only Australian Header manufacturer to manufacture their products with Pipe Over Cone™ technology copyright number 135712 applies.
- The advantages of Pipe Over Cone™ technology are there is no protruding pipe inside the collector cone, therefore increasing exhaust gas flow and eliminating turbulence inside the exhaust header.
- The result is better gas flow and increased horse power.
Helpful Hints
- Read the instruction sheet supplied with the headers.
Disconnect the battery. - On E.F.I. computer controlled vehicles, use anti-zap device on the battery before welding to prevent spiking the computer.
- Make sure the head face is clean before fitting the headers.
- Use non-silicon based sealant on the face of the header E.F.I. vehicles.
- Do final check to ensure ignition leads, clutch cables, power steering lines and Auto cooling lines are clear of the headers.
-
Mandrel Bend
This type of bending system allows the tube to be bent, without altering its original shape and size, which in turn enhances flow and appearance. Some header manufacturers do not have access to this system while others mix and match mandrel bends with ordinary press bends. At PACEMAKER, every bend is a mandrel bend.
-
Pipe Over Cone
Traditionally, header manufacturers welded protruding secondary and outlet pipes to manufacture headers. At PACEMAKER, we developed the pipe over cone technology (copyright number 135712). All PACEMAKER headers are manufactured with the pipes flared and welded over the collector cone, so nothing protrudes inside the collector cone, therefore increasing exhaust gas flow and eliminating turbulence inside the exhaust header. The result is better gas flow and increased horsepower.
-
All Pipes Fitted Through the Flange
There are two ways pipes can be welded to a flange. The correct way which is the way PACEMAKER headers are manufactured, is to have the pipe set through the flange, welded around the top to seal the pipe, mould the pipe to the correct size and shape and then finally, machining off the access. The other way is to simply butt weld the pipe onto the top of the flange. This may seem to be the easiest way of welding pipes to a flange but unfortunately, this means the flange port needs to be cut smaller than the pipe and not necessarily to the right size and shape to match the cylinder head.
-
A Quality Finish
At PACEMAKER, we believe that the product should not only perform well but have a high quality finish too. Everything from the attention to detail of our designs to the clean appearance of our welding technique to the use of smoother mandrel bends and precision laser cut flanges all combine to help make PACEMAKER headers one of the highest quality headers on the market today. And to set them off, PACEMAKER headers are finished in a bright and attractive, specially developed blue heat proof coating that will last well into the header's life. There is more to the finish than meets the eye.